本文转载自“医药观澜”。
曾几何时,生物药被视为欧美企业的专利。生物药制备环节繁多复杂,质量体系要求极高,达到国际一流标准殊为不易。2018年以前,走出国门的“中国造”生物药还是一片空白。
但在去年,这个格局被打破——由中裕新药创制、药明生物生产的创新艾滋病疗法Trogarzo(ibalizumab-uiyk)获得美国FDA批准上市,这是首例在中国生产、并得到FDA批准在美国上市的无菌生物制剂。进一步的好消息是,不久前,药明生物顺利完成该产品上市后的首次FDA GMP例行检查,并通过了欧洲药品管理局(EMA)的药品上市批准前检查(PAI),成为中国首家获得美国FDA和欧盟EMA GMP双重认证的生物制药公司。
药明生物的异军突起,正是中国医药行业快速发展,融入全球医药生态的缩影。近日,药明生物首席执行官陈智胜博士在接受访谈时表示,“我们希望向行业传递一个信念:国际标准并非高不可攀,中国企业也能够做到。”
▲药明生物首席执行官陈智胜博士
一步都不能错!
放眼全球,生物药是当下创新疗法开发的重点。近6年来美国FDA批准的单抗药物数量呈稳定上升之势。这些作用机理与传统小分子药物截然不同的疗法为全球病患带来了全新的治疗方案,但也在生产工艺和质量等领域面临多重挑战。
不同于小分子药物生产过程的高度可控,生物药由于分子结构复杂,用以生产生物药的活细胞对外部环境相当敏感,制备过程充满考验。生物药的原液生产对稳定性的挑战极高,制剂过程需要保证绝对无菌;再者,生物药的生产通常历时数十天,环环相扣,容错率极低。以Trogarzo为例,“它的生产周期约40天,涉及近50种原料,环境、物料、人员,一步都不能错。”陈智胜博士举例说道。
除了工艺复杂,ibalizumab早期几经易主,如何重现制备技术也是巨大的难题。Ibalizumab开发于90年代,彼时用于表达抗体的细胞株是相对陈旧的NS0细胞,使用的生产设备还是不锈钢发酵罐。至2012年这项合作起步时,一次性生产技术逐渐成为行业趋势。一次性生物反应器的优势是显著的,不仅有助于避免污染、更有安全保障,又能够快速切换批次、高效生产,还无需频繁清洗,节约成本。然而,基于当时的文献资料,NS0细胞被认为不适合在一次生物反应器中进行培养。药明生物团队在初步探索时也确实出现了这一情况。
通过评估不同厂商、不同材质的一次性生物反应器,并与设备厂商不断探讨,团队几经探索,最终成功在一次性生物反应器中转移了细胞培养生产工艺,并顺利放大工艺成功生产了ibalizumab。
此后,药明生物携手合作伙伴向国际标准看齐,反复推敲每一个工艺细节,针对差距逐一寻找解决方案。“从2015年工艺申报到2017年FDA批准前检查,上千页的批生产记录更新了10个版本,近两年,又有不少工艺技术文件调整了4-5版。” 陈智胜博士补充道。Ibalizumab的工艺优化过程,伴随着药明生物质量体系的建设和完善,陈智胜博士也将此戏称为“一边造飞机,一边开飞机。”
当然,了解国际监管法规、执行国际标准都离不开专业人才团队的建设。在这个过程中,药明生物持续吸纳经验丰富的国际化人才,并引入了曾在FDA任职近30年的资深专家辛强博士担任公司首席质量官及其他专家顾问加盟。
艰难困苦,玉汝于成。在接受欧美药品监管机构三次现场检查的过程中,药明生物均无任何数据完整性问题。同时,陈智胜博士也坦言,生物药生产的复杂性,决定了质量始终都有提升的空间。“从80分到100分的挑战尽在细节,越往后越难,这是一个无限逼近完美的过程。”
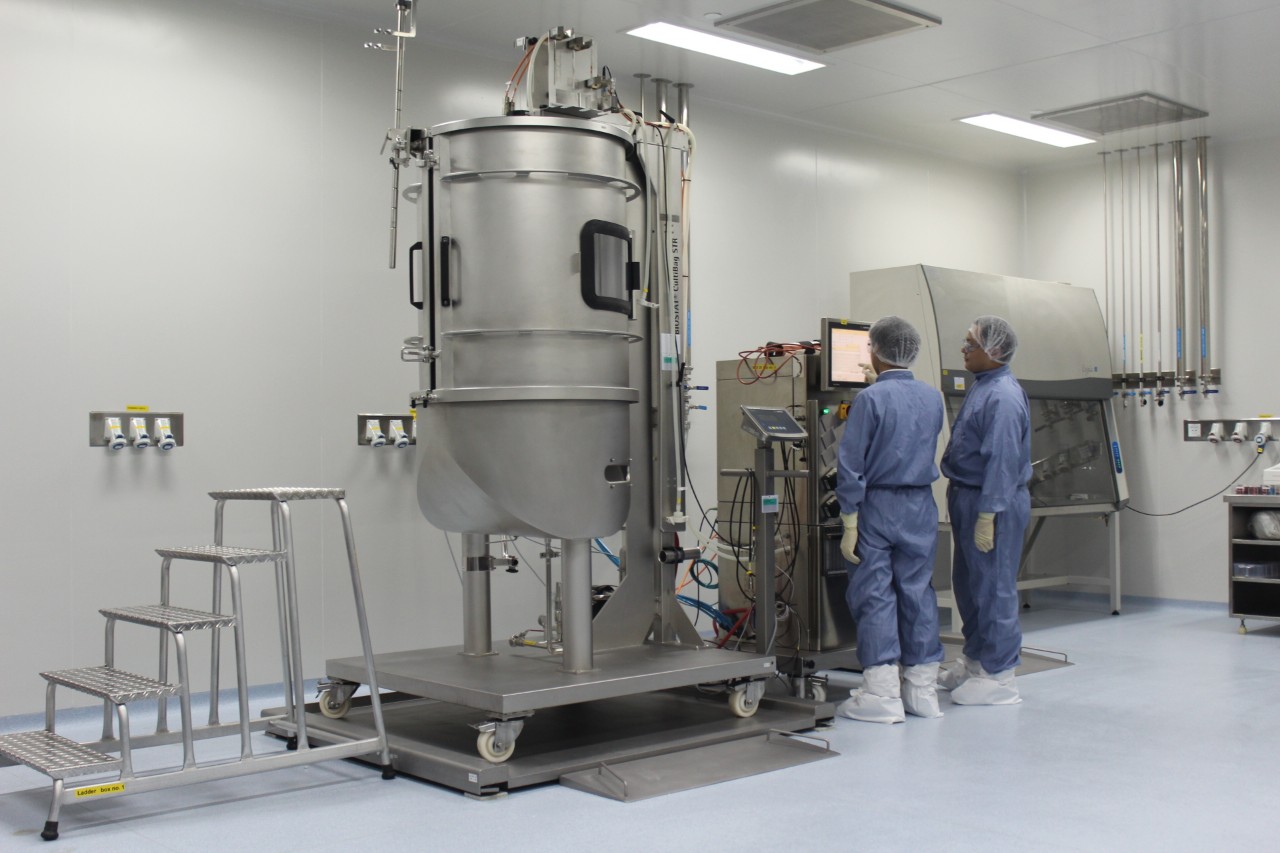
▲研究人员在为ibalizumab生产调试
“产能建设”助力“创新药物可及”
如今,生物药应用于越来越多的疾病领域,而不同治疗领域对生物药的产量需求也千差万别。有数据统计,为了满足众多肿瘤患者的治疗需求,PD-1/PD-L1单抗每年的产量都以吨计!相反,治疗罕见病的药物生产需求量就非常少,一款抗体孤儿药可能一年只需要生产100g。
另一方面,从早期研发、临床试验到商业化生产,产能管理在药物生命周期的作用也不容小觑。随着MAH制度试点在国内深入推进,生物药企业对产能建设也衍生了更多潜在需要。
显然,应对市场需求的多样变化,满足不同产能需求的生产设备就显得尤为重要。
为了更快实现不同规模灵活生产,药明生物创造了一种新的模式:“组合”多个一次性生物反应器,以此取代“放大”单个不锈钢生物反应器容量。目前,药明生物的生产基地拥有多种不同规模的一次性生物反应器,能够以50升-12000升的生产线同时生产十种生物药。
在灵活和迅速的生产服务的基础上,要支持更多生物药的研发和生产项目,并更进一步为合作伙伴带来规模效益,还离不开产能的持续扩大。药明生物在商业化生产中率先应用一次性反应器来扩充总产能,通过后续建设,到2022年总产能预计将达到22万升。
为了实现更高的产率,进一步降低生产成本,药明生物也在不断改进细胞培养工艺,研发新一代的解决方案。比如在WuXiUP(无上)创新平台上,大致相同的细胞培养周期内,产量是传统培养方式的5-10倍,运用1000升一次性生物反应器一年可以生产500kg的单克隆抗体!这对于抗癌单抗等应用广泛的药物来说,可以满足大量患者的需求。
“通过提升产能和批次生产效率而摊薄生产成本,可以帮助更多百姓用得上药,用得起高质量生物药。”陈智胜博士补充道。
▲药明生物车间照片
更多疗法,更快研发
得益于满足国际标准的质量体系以及领先的技术能力,药明生物赢得越来越多全球合作伙伴的信任,正在为全球约1/7的生物药研发生产提供技术平台。截至2018年底,药明生物平台上的研发综合项目达205个,包括131个传统抗体,31个融合蛋白,19个抗体偶联药物,10个双特异性抗体,以及十余个酶、细胞因子等药物。近日,药明生物与全球疫苗巨头最新达成合作意向,为一款创新性疫苗提供生产,服务全球市场。由于疫苗的生产难度和质量控制要求颇高,疫苗领域的合作生产案例并不多见,此项合作也开创了疫苗行业全新合作模式。
陈智胜博士提到,从药明生物平台的大量在研项目中也能看到行业趋势。当下,生物药研发大多聚焦于肿瘤和自身免疫系统疾病领域,同时也正拓展至更加广泛的治疗领域,如传染病、罕见病、中枢神经系统疾病等。令人欣喜的是,中国力量也逐渐崭露头角,现阶段平台上共有十余个中国原创、first-in-class的全球新药,在最高质量标准下,药明生物希望赋能更多本土创新药走向国际市场。
除了多个领域都有大量研究涌现,行业对创新疗法的开发速度也不断寻求突破。传统单抗从发现到临床申报,通常需要15-24个月,而依托药明生物规模领先的WuXia(无瑕)细胞系平台,这一周期得到大幅缩短。Tychan公司在此平台上针对寨卡病毒和黄热病毒开发的两款首创单抗,从细胞株构建到临床申报分别历时9个月和7个月,一再刷新行业记录。此外,WuXiBody™平台则突破了双特异性抗体的技术瓶颈,有望为每个项目节约6到18个月研发时间,天境生物、韩国ABL Bio、英国Oxford BioTherapeutics等公司正在该平台上推进多个双特异性抗体的研发进程。
一系列高速发展也为药明生物在中国其他地区、爱尔兰、新加坡、美国的生产基地打下了坚实基础,并进一步支持“药明生物提供全球双厂生产”的策略。在业内,一款生物药两地生产较为普遍,而不同生产企业往往难以统一质量标准,这一策略有望在降低技术转移风险、满足多国监管要求等方面,为合作伙伴带来独特的解决方案。陈智胜博士表示:“药明生物将继续通过健全强大的全球供应链网络,确保为合作伙伴提供符合国际最高质量标准的服务,造福广大患者。”
后记
谈及未来3-5年生物药领域的突破方向,陈智胜博士提出了“成本”这一行业课题。药物研发是成本最高昂的商业活动之一,提高新药研发效率已经成为全球行业挑战。根据德勤发布的一项报告,2018年推动一款新药上市的所需成本已经是2010年数值的两倍;而维持这一创新生态系统运转的成本也会反映在患者端,创新药的可负担性在大多数国家都是行业主要挑战之一。
在陈智胜博士看来,持续的技术创新、开放技术平台,正是提高研发和生产效率,降低投入、解决患者药物可及问题的潜在方式。我们看到,从实现抗体药首次走出国门的里程碑,到为全球1/7的生物药研发生产提供平台,药明生物正在赋能越来越多创新生物药研发企业,加快和变革全球生物药的开发和生产进程,把更多高质量创新生物药尽早带到全球患者身边。